Blog
Improve Collaboration with Kanban for Vendor & Supplier Management10 Jul 2024
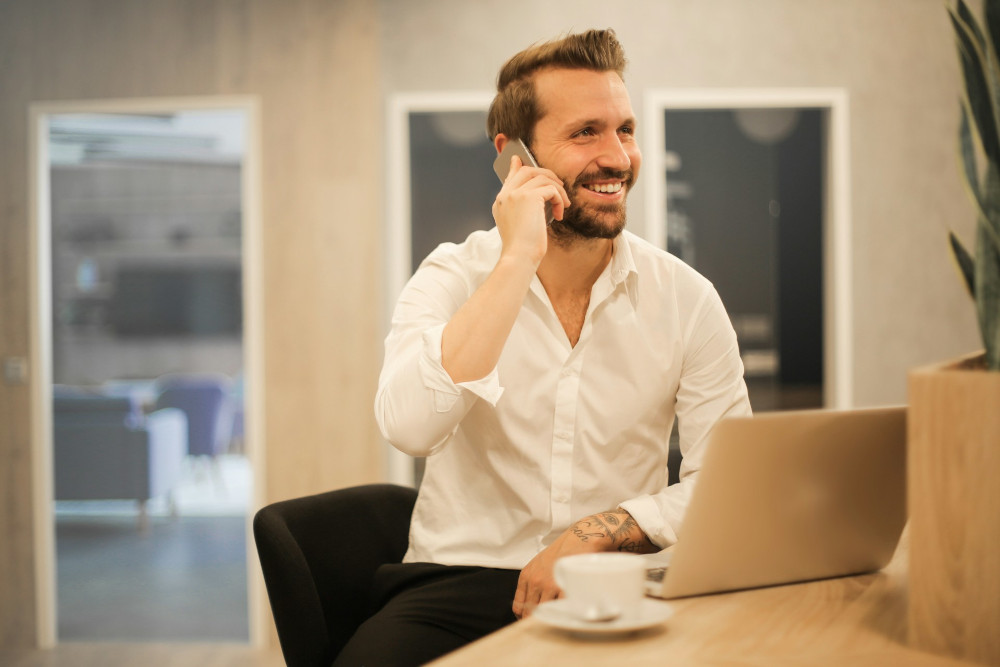
No matter what your business does, effective vendor and supplier management is critical to maintaining a competitive edge. Kanban, the visual workflow management method originating from lean manufacturing, offers a robust solution to streamline and optimize these processes. By leveraging Kanban principles, your business can increase efficiency, improve communication, and foster stronger relationships with suppliers and vendors.
Understanding Kanban
Kanban, a Japanese term meaning signboard, was developed by Toyota to improve manufacturing efficiency. It involves visualizing work, limiting work in progress (WIP), and managing the flow of tasks. Kanban boards, be that physical or digital workflow illustration, display tasks as cards moving through stages of completion, for instance, through the classic To Do - In Progress - Done columns. This highly visual representation can allow your team to see the status of tasks at a glance, identify bottlenecks, and continuously improve the process.
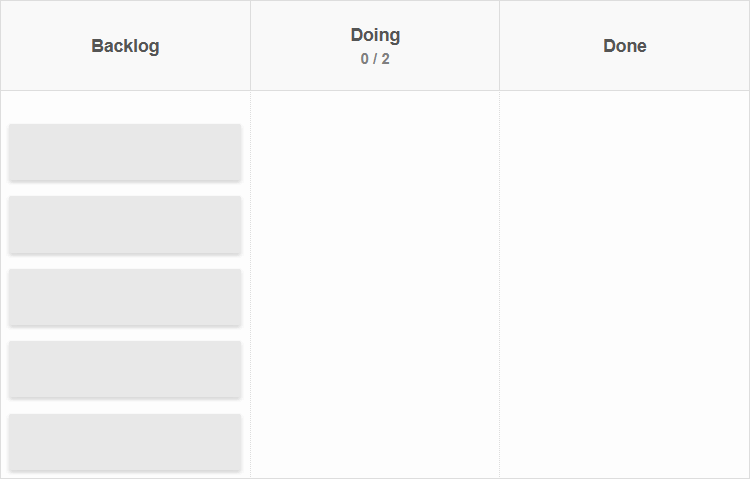
How to Apply Kanban to Vendor Management?
1. Visualize the Workflow
A Kanban board can be adapted to represent various stages of vendor and supplier management, depending on your unique business flow. For example, it might look as follows:
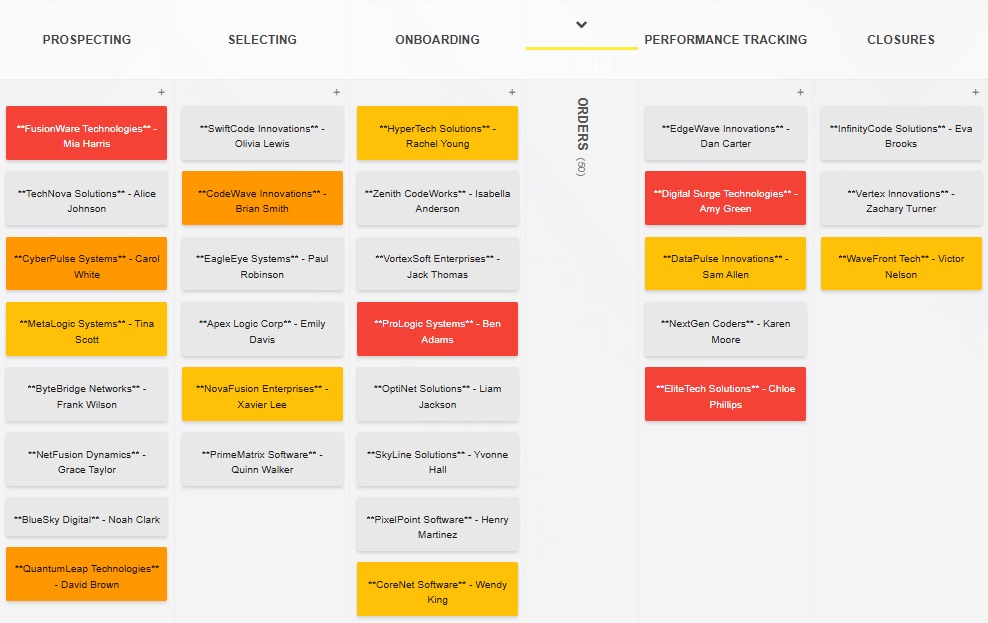
- Prospecting: Identifying and evaluating potential new vendors, including tasks related to identifying specific needs, doing market research, and running initial vendor assessments.
- Selecting: Requests for Proposal (RFP) reviews, vendor interviews, and due diligence.
- Onboarding: Negotiating contracts, setting up accounts, integrating systems, or introductory meetings.
- Order Placement and Management: Placing orders, tracking shipments, and managing inventory.
This step, as potentially holding the highest number of tasks, could be split into Placed, Processing, Shipping, Received, and Closed. - Performance Tracking: Assessing vendor performance and compliance, tracking ongoing relationships, managing contract changes, and addressing any issues that arise during the contract period.
- Contract Closure: A final column to cover tasks related to contract completion, vendor evaluation, and closing out engagements.
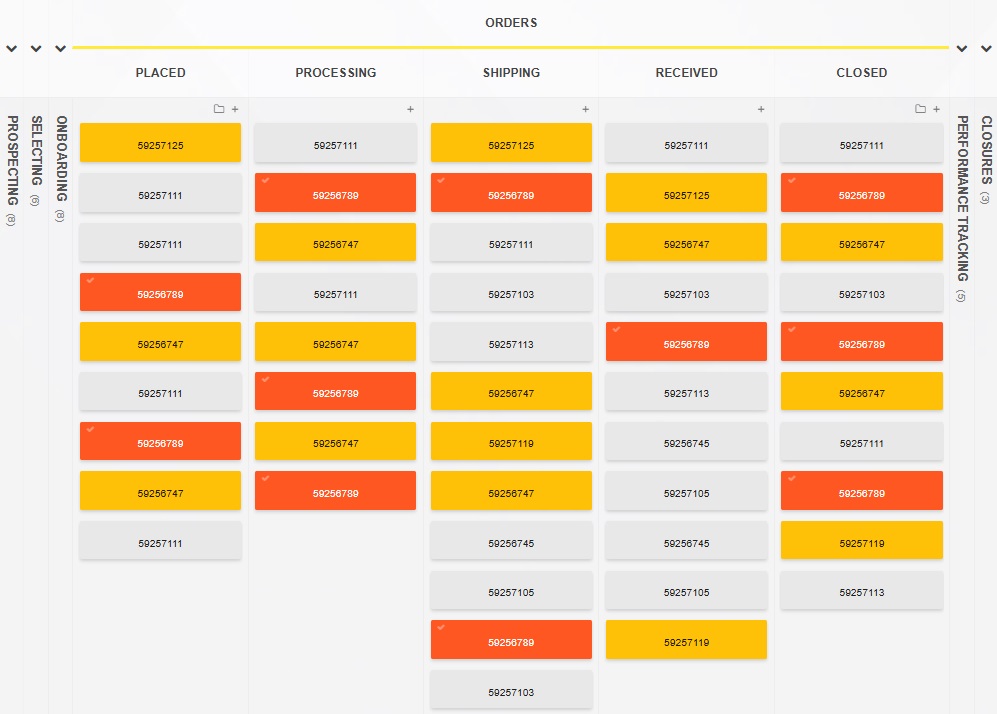
By visualizing these stages, your company can gain a clearer understanding of your supplier workflow, making it easier to identify areas for improvement.
2. Limit Work in Progress (WIP)
Limiting the number of items in progress at one time is a core principle of Kanban, which prevents overloading the system and improves focus. By interacting only with a manageable number of vendors and orders at a time, your company can ensure that each order and vendor, receives adequate attention, reducing the risk of errors, delays, and miscommunication. This approach could also help in maintaining a balance between demand and capacity, ensuring smoother operations.
3. Manage the Flow
A smooth, continuous flow is both recommended and possible with Kanban. For supplier management, this would translate to minimizing delays and ensuring timely delivery of ordered goods and services. By tracking the flow of tasks on the Kanban board, your team can quickly identify and address bottlenecks, such as delays in order processing or shipment tracking. Continuous monitoring of the process state and the improvements that follow, help maintain a consistent supply chain, boosting your company's reliability and reputation.
Benefits of Kanban for Vendor Management
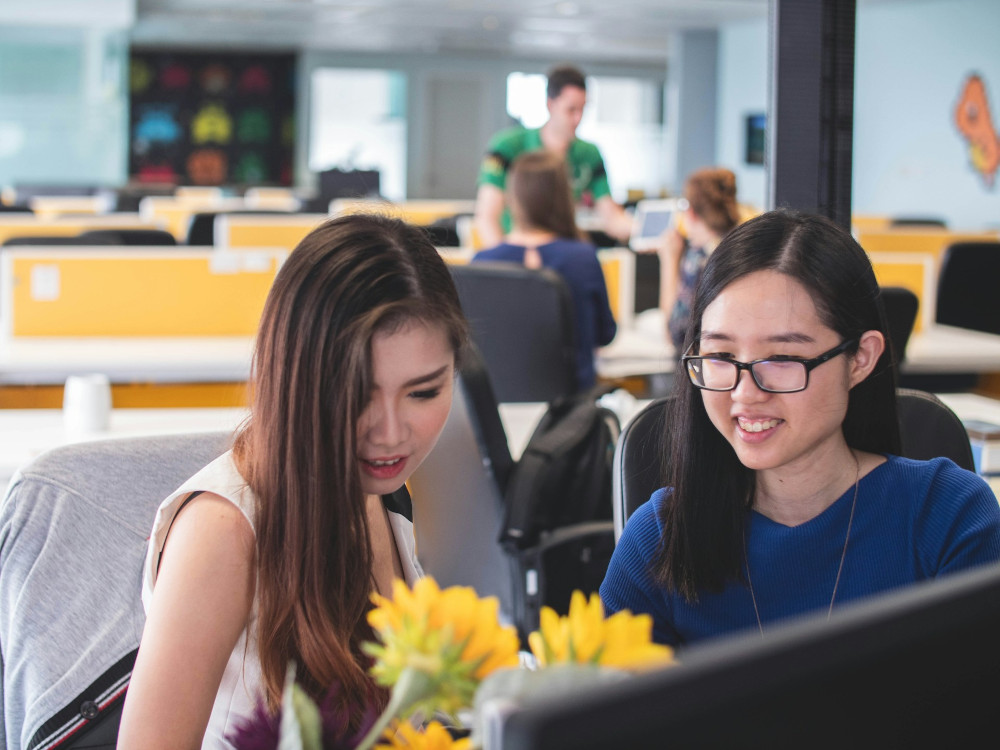
Higher Process Transparency
The transparent insight into the entire vendor management process allows all stakeholders, from procurement teams to senior management, to understand the status of tasks, orders, and vendor relationships and identify potential issues early. Enhanced transparency fosters better team communication and collaboration, leading to more informed decision-making.
Improved Efficiency
By visualizing and sharing the workflows, limiting WIP, and effective flow management, Kanban helps identify inefficiencies in the processes. It can lead to faster turnaround times, reduced lead times, and overall efficiency improvement in vendor and supplier management. With that, your company can better allocate resources, manage inventory, and meet customer demands more effectively.
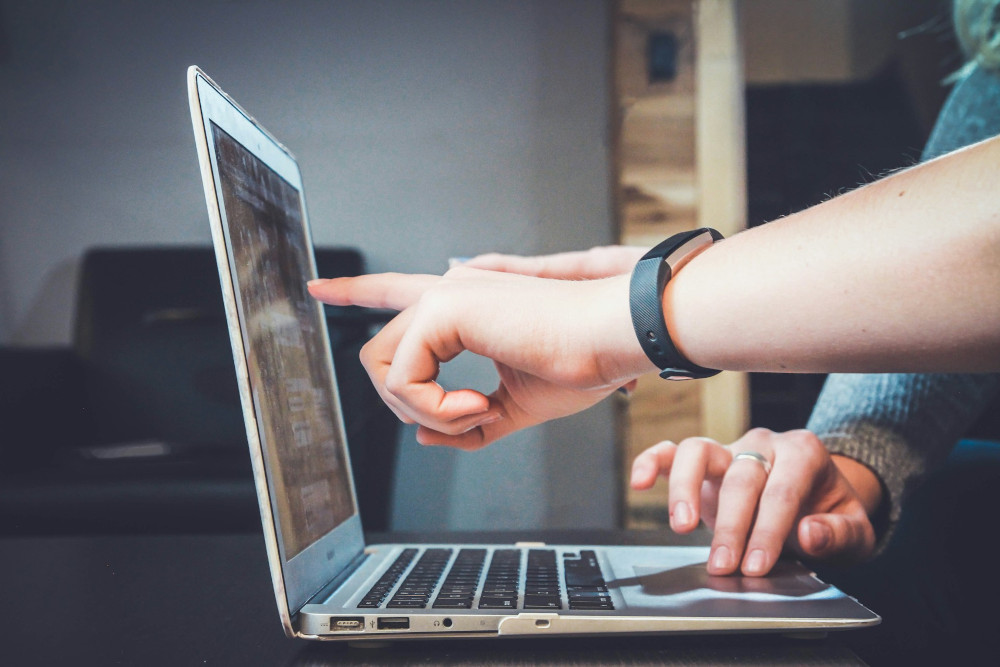
Better Vendor Relationships
Kanban encourages continuous improvement and proactive problem-solving, as by addressing issues promptly, your company can build stronger, more collaborative relationships with vendors and suppliers. Such a collaborative approach leads to better negotiation outcomes, improved service levels, and long-term partnerships that benefit both sides.
Increased Agility
Within the highly unpredictable, ever-changing business environment, business and procurement agility is crucial. Kanban enables your company to respond quickly to changes in demand, supply chain disruptions, or changing market conditions. The ability to adapt and re-prioritize tasks based on real-time data will ensure that your business remains resilient, competitive, and current.
Implementing Kanban in Vendor and Supplier Management
To successfully implement Kanban, consider following these steps:
- Set up a Kanban board: Choose a physical or digital board and define the stages of your vendor management process. For a distributed team and high-volume flows, an online board such as kanbantool.com will be most convenient.
- Define WIP limits: Determine the maximum number of tasks allowed in each stage to prevent overload. Generally speaking - the lower the limit, the better.
- Visualize tasks: Represent work with tasks, providing all the detailed information and deadlines.
- Monitor and adjust: Regularly review the board, identify bottlenecks, and make adjustments to improve flow. Going with a Kanban Tool board will yield the added benefit of automatically generated process metrics, such as time reports, cumulative flow charts, breakdown charts, and a lead and cycle time diagram.
- Foster a continuous improvement culture: Encourage all team members to provide feedback and suggest improvements to the process.
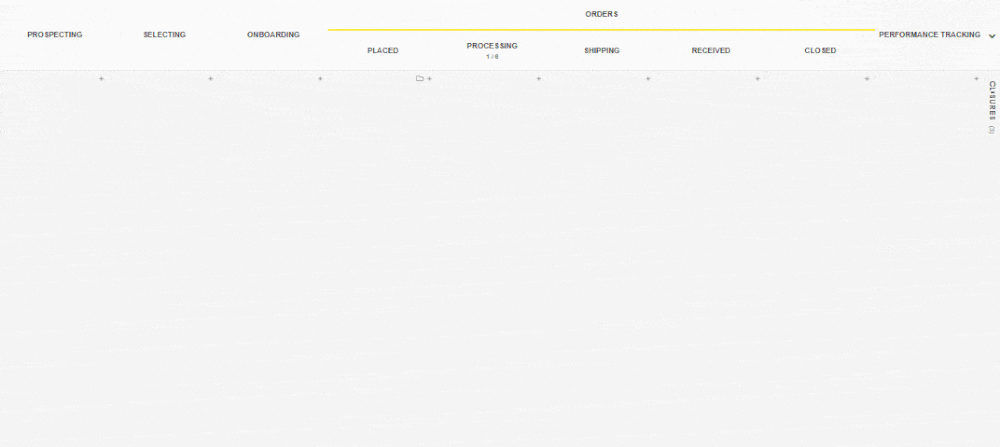
Conclusion
Kanban offers a mighty, visual approach to vendor and supplier management, providing much-needed order and structure, thereby enhancing transparency, efficiency, and collaboration. By implementing Kanban principles, your business can streamline all workflows, build stronger vendor relationships, and stay competitive. While embracing Kanban usually starts with adopting a new tool, it should later expand onto fostering a culture of continuous improvement and agility that drives long-term success.
Sign up for a 14-day free trial
to test all the features.
Sign up now and see how we can help
your organization deliver exceptional results.