Blog
Mastering Efficiency – Kanban and Lean Fusion for Seamless Business Operations13 Feb 2024
Tackling business process streamlining can feel overwhelming amidst all the available methods, tools, and advice. But there is an approach that can optimize efficiency without hefty investments or a lengthy timeframe - it's the combination of Lean practices with the Kanban method.
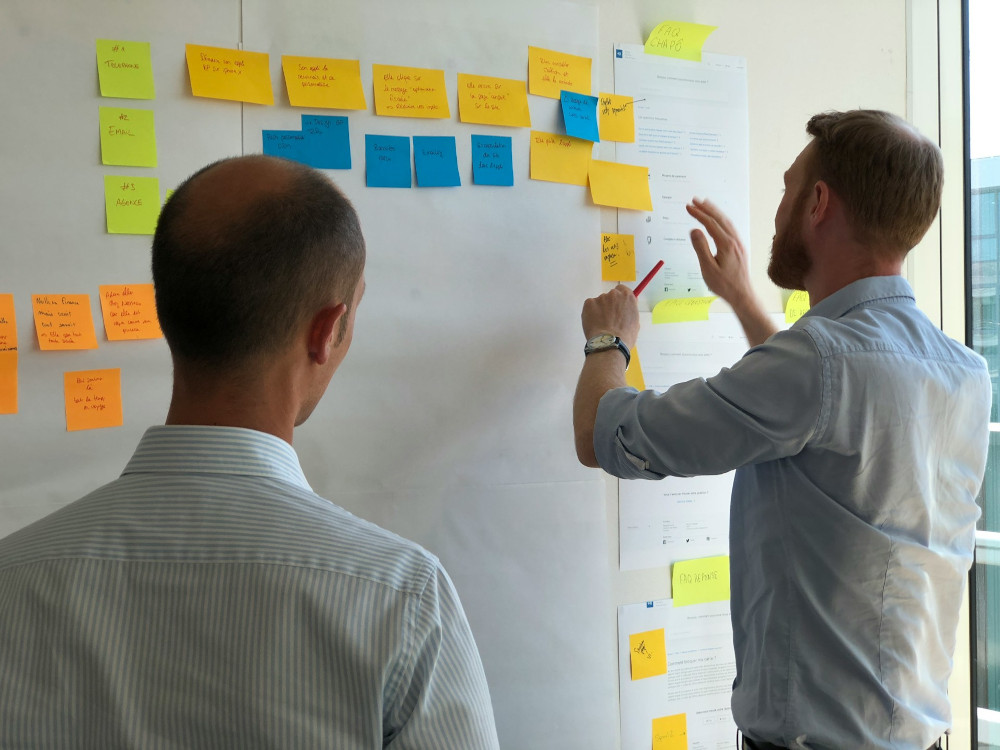
What are Lean and Kanban?
Lean is a flexible business approach that aids in achieving goals sustainably, comprising continuous improvement and respect for people. Through that, Lean aims to maximize customer value while minimizing waste.
Higher customer satisfaction and increased value delivery can be achieved through a structured work approach, emphasizing transparency, communication, collaboration, focus, and clarity. Enter Kanban - a visual workflow management method providing organizations with the visibility and focus necessary to manage work and teams effectively. Project management hands-on realization of Kanban is usually done through a visual Kanban board, focused on the needs of a project, team, department, or an operational process, on which the team sets out their goals and tasks, moving them across the process steps for real-time status sharing among everyone involved.
In short, Kanban and Lean principles share a common goal: to eliminate waste and optimize processes. Merging these two approaches helps organizations create a capable framework for continuous improvement and efficiency.
How do Lean and Kanban synergize to improve your process?
- Visual Management
Kanban emphasizes illustrating work through boards and cards, making it easy to see the workflow and identify bottlenecks. Lean principles also advocate for visual management to ensure transparency and facilitate communication. By visualizing workflows and processes, your team can quickly identify areas of waste and opportunities for improvement while also gaining insight into the process as a whole. Complete process visibility gives you an unprecedented chance to align everyone in the company around a shared view of reality - with its goals, problems, and current status. - Limiting Work in Progress (WIP)
Kanban and Lean stress the importance of limiting WIP to avoid overburdening teams and improve flow. By setting WIP limits based on available capacity, your teams can focus on completing tasks efficiently without spreading themselves too thin, putting 100% of their effort into the task at hand. That will lead to faster cycle times and reduced lead times, ultimately enhancing your customers' satisfaction and flow predictability. If you're curious about how WIP limits work, try them on a shared Kanban Tool process management board. - Continuous Improvement (Kaizen)
The Lean philosophy promotes a culture of continuous improvement, or Kaizen, where every team member is encouraged to identify and implement small, incremental process changes. Kanban supports this by providing a feedback loop through regular retrospectives and metrics tracking. Your team can use Kanban boards to visualize performance analysis and identify areas for improvement, fostering a culture of experimentation and learning and promoting work accountability and ownership. - Just-in-Time (JIT) Delivery
Lean advocates just-in-time delivery, where your goods or services are produced or delivered only when needed, minimizing inventory and waste. Kanban's pull-based system aligns with JIT principles by enabling your team to pull work only when there is capacity, minimizing the risk of overproduction and unnecessary inventory buildup. It can lead to more efficient resource utilization and lower carrying costs. - Respect for People
Lean philosophy emphasizes respecting people and their expertise, while Kanban promotes a collaborative and empowered team environment where individuals have autonomy and are trusted to make decisions. By fostering a culture of respect and empowerment, your organization can leverage the team's collective intelligence to drive innovation and problem-solving, at the same time increasing employee job satisfaction and knowledge growth. - Value Stream Mapping
Value stream mapping is innate to Lean, as it helps to identify and eliminate waste across the entire value flow. Kanban complements this by providing a granular view of individual workflows and processes, which you can then analyze and optimize as part of the broader value stream. By understanding your end-to-end flow of value and eliminating non-value-added activities, your company can streamline processes and improve overall efficiency.
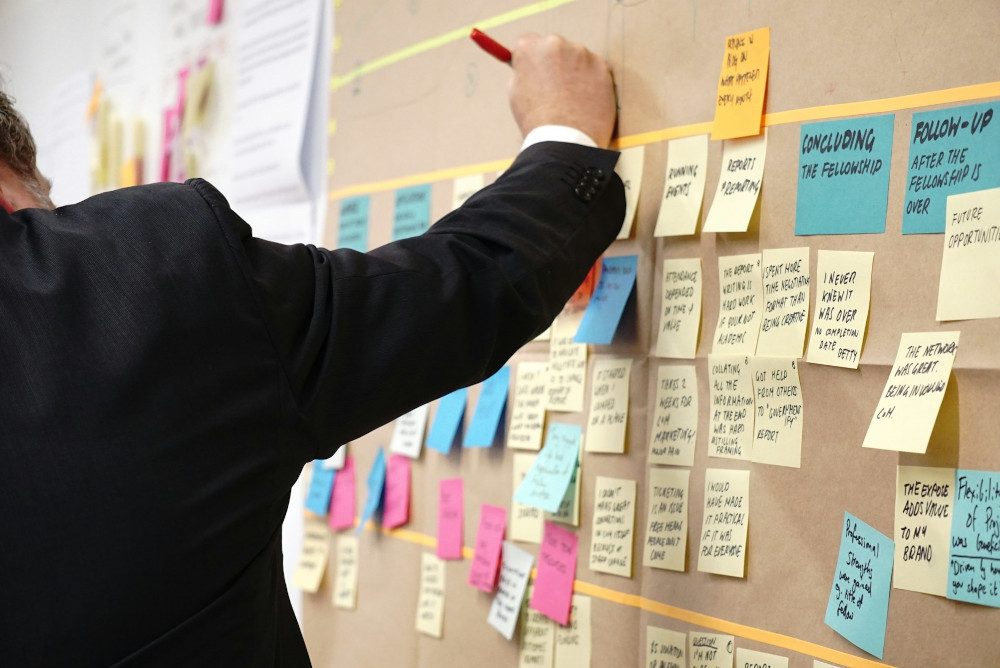
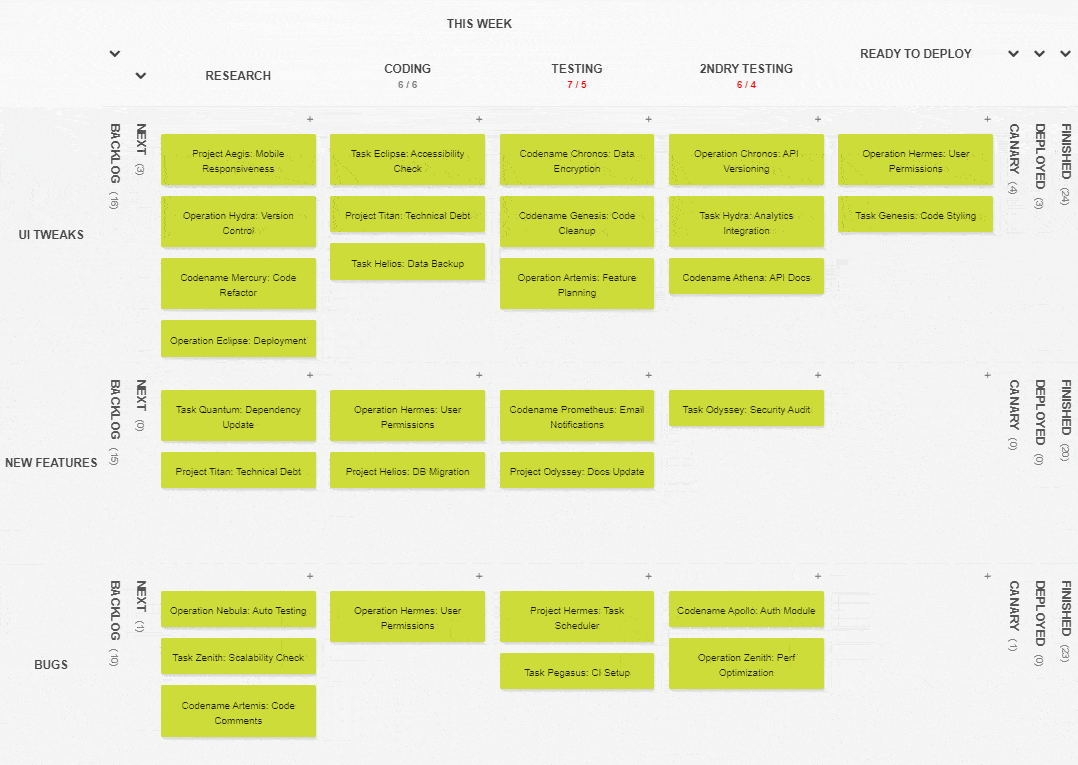
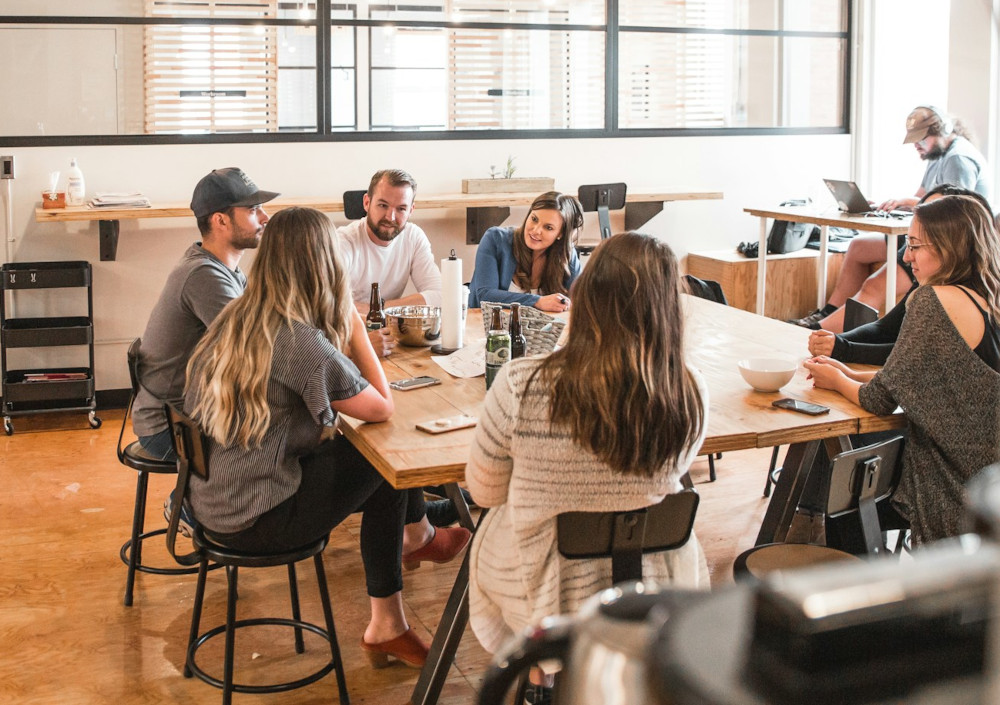
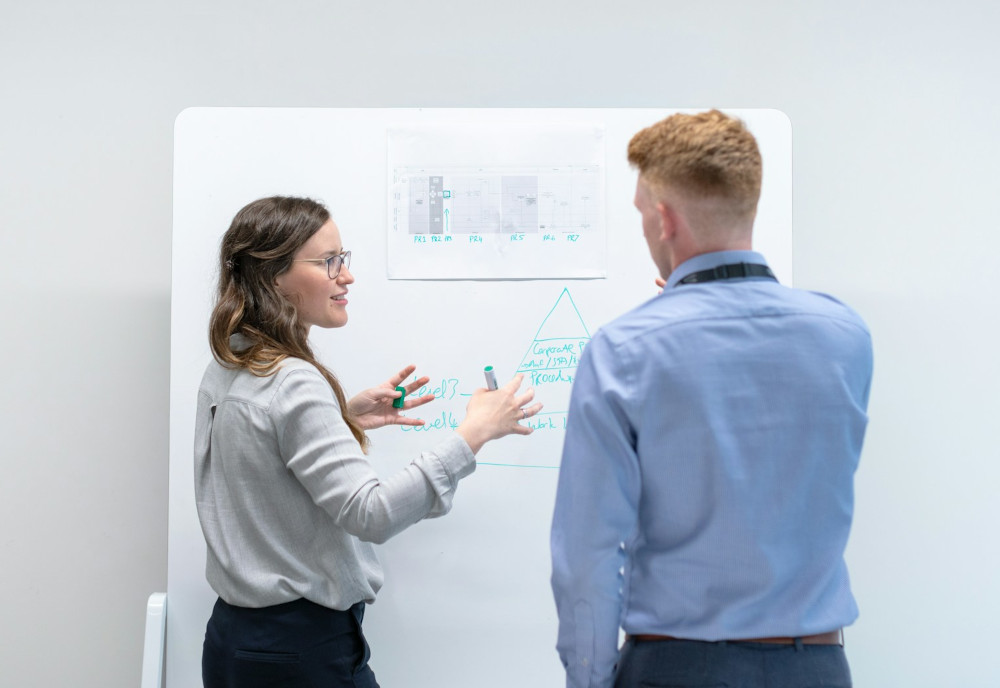
As you can see, integrating Kanban and Lean principles can help you create a holistic approach to process optimization that fosters continuous improvement, enhances collaboration, and ultimately delivers higher value to your customers!
Sign up for a 14-day free trial
to test all the features.
Sign up now and see how we can help
your organization deliver exceptional results.